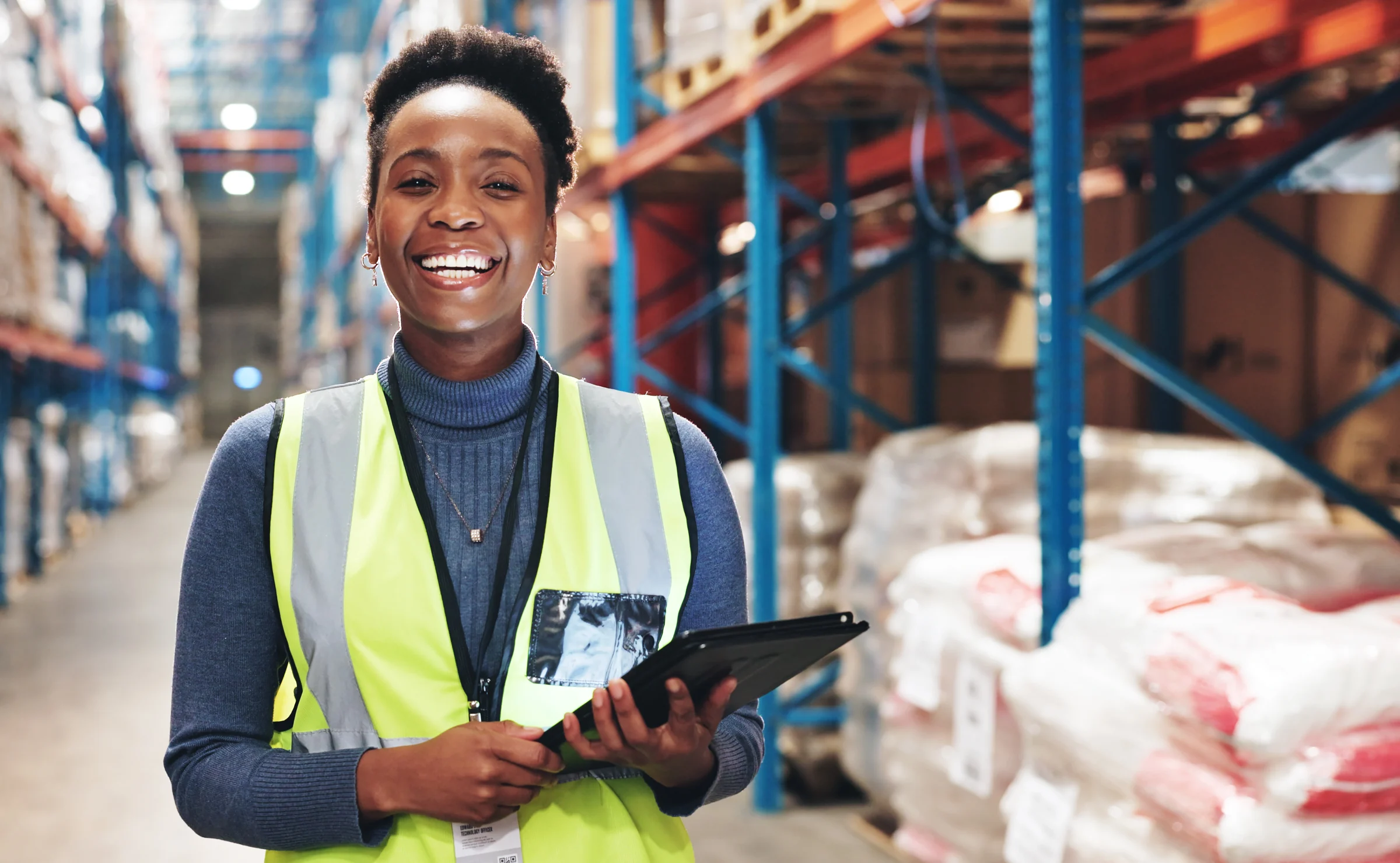
A packing slip is a document that accompanies an order and serves as a record of the goods delivered. It is an essential part of the logistics process, both for businesses and consumers. In this article, we will dive into the details of what exactly a packing slip is, why it is important and how you can optimise the processing of packing slips.
A packing slip lists all the products included in a delivery. The document is added to the shipment by the supplier and can be used by the recipient to check that the delivery is complete and correct. It usually contains the following information:
- Supplier contact details: Name, address, and possibly a telephone number or e-mail address.
- Order number: This number refers to the original order.
- Description of items: For example, item codes, quantities, and sometimes a short description.
- Shipping date: When the order was shipped.
- Missing items: If part of the order has not yet been delivered, this is often also mentioned.
So a packing slip is not the same as an invoice. An invoice is a legal document used to enforce costs, while a packing slip can be important for other reasons.
Why Important?
The importance of a packing slip cannot be underestimated, especially in a business context. Here are some reasons:
- Verification of Deliveries: It acts as a checklist to verify that all items ordered have been delivered.
- Efficiency in Logistics: Clear indication of content makes it easier for warehouse staff to process deliveries.
- Customer service: In case of any complaints, the packing slip can be used as a reference.
- Proof: If discussions arise about what has or has not been delivered, the document serves as proof.
How to Process?
For companies handling physical goods, processing a packing slip is an important process. Here are some steps to make this process run smoothly:
- Receipt of Delivery: When the delivery arrives, start by checking the document. Make sure it is kept with the shipment.
- Check the Items: Compare the information on the document with the goods delivered.
- Processing in the System: Use a solution like TriFact365 to include relevant data in your records. This helps with inventory management and invoicing.
- Report Deviations: If something is wrong, report it to the supplier immediately. Use the packing slip as the basis for your communication.
- Retain: Archive the packing slip as evidence. This can be physical or digital, depending on your workflow.
Tips for efficient management
- Digitise the Process: Use a digital solution to scan documents and process them directly into the system. This saves time and prevents errors.
- Use Barcodes: Suppliers can use barcodes for faster processing.
- Automate Inventory Management: Link your packing list processing to an inventory management system to allow real-time updates.
- Check Supplier Systems: Choose suppliers that provide clear and straightforward packing slips.
A packing slip is much more than just a list of products. It is an important document for streamlining logistics processes and increasing customer satisfaction. By optimising processing, you can save time and minimise errors. Make sure your systems are set up properly and keep looking critically at improvements in your workflow.